Aluminum is an essential material in a wide range of products used in many areas, from packaging to aviation vehicles today. As in all production processes, environmental resources are utilized in the steps required for aluminum production, and production residues are given to the environment. It is desirable that the emissions of the aluminum industry be halved by 2050.
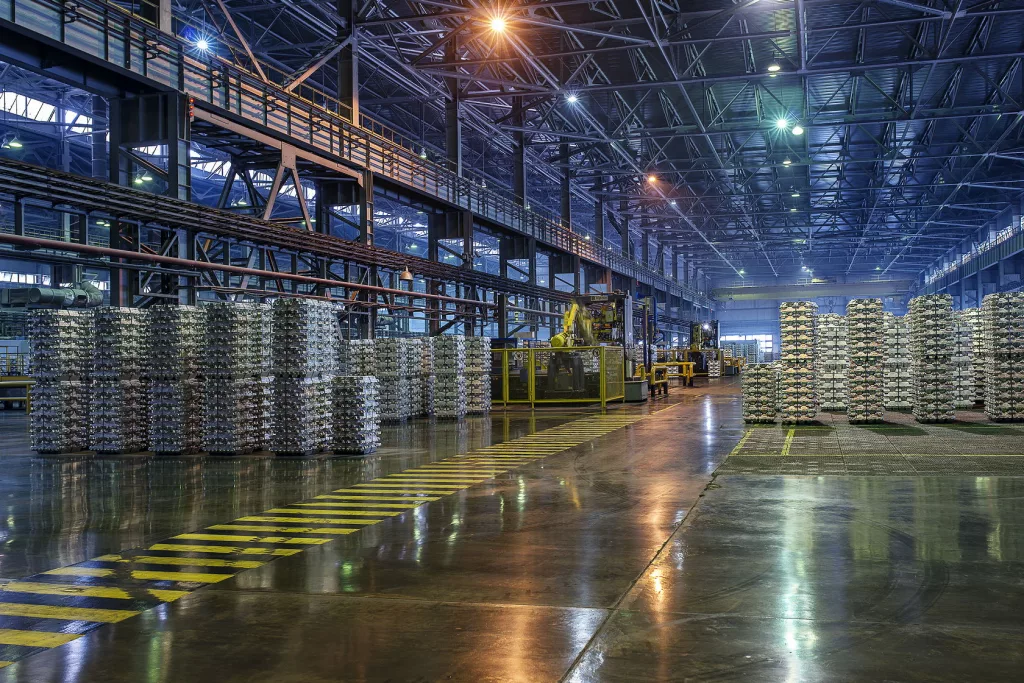
After iron, aluminum is the second most widely used metal globally. The element aluminum is abundant in the world and is taken from nature in the form of bauxite mineral, which constitutes 8% of the earth’s crust (Çakanyıldırım & Gürü, 2021). There are various minerals in the world from which aluminum can be obtained, but the most common raw material is bauxite. Bauxite is a mineral consisting mainly of aluminum oxide, which is mixed with some other minerals. Bauxite is considered high quality if it contains more than 50% aluminum oxide. Around 90% of the global bauxite supply is in tropical and subtropical regions, while 73% is in only five countries: Guinea, Brazil, Jamaica, Australia, and India (Abaout Aluminium, 2022).
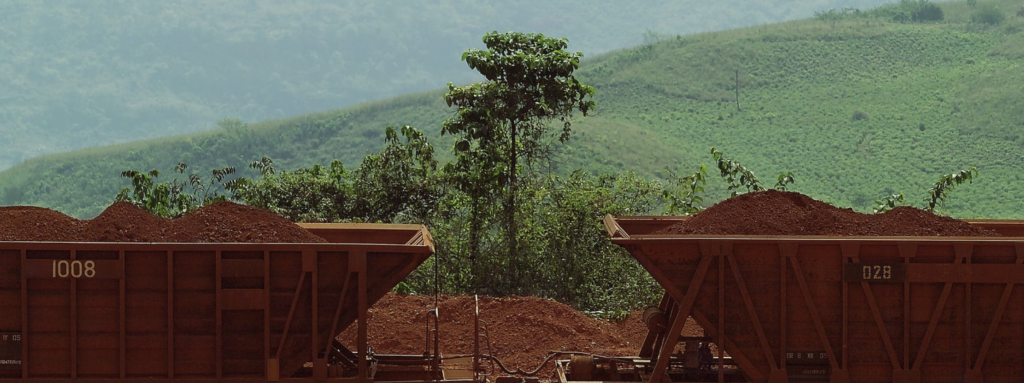
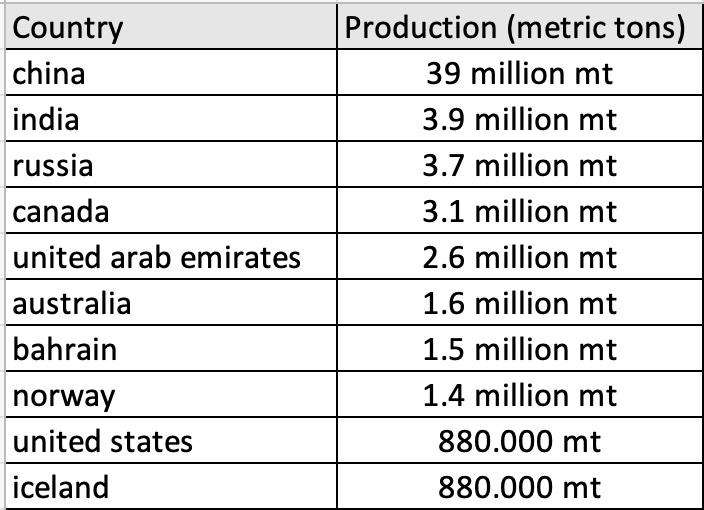
Most of the leading countries in aluminum production are in last place in terms of bauxite reserves. Canada, for example, which has no bauxite reserves, ranks third in the world, producing primary aluminum in many countries based on imported ore (Eroğlu & Şahiner, 2018).
Aluminum is a 100% recyclable material without losing its original properties. Aluminum produced from the bauxite mine is primary, and aluminum recovered from scrap is secondary.
Traditional primary aluminum production consists of three processes that are independent of each other (Metal World, 2018):
- Bauxite mining,
- Production of alumina from bauxite ores by Bayer Process,
- Production of metallic aluminum from aluminum by “Molten Salt Electrolysis (Hall-Herault Process).
Alumina refining and aluminum smelting are responsible for over 90% of aluminum production’s direct CO2 emissions, the rest being from recycled production, anode production, and casting (IEA, 2022).
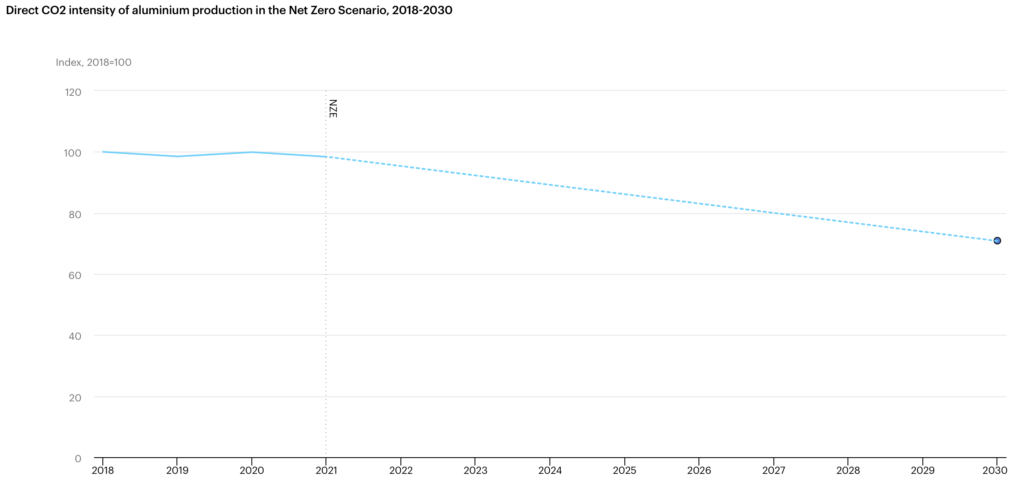
In particular, the electrolysis stage of molten salt is energy-intensive. While energy cost constitutes approximately 40% of the price in primary aluminum production, The share of energy in total expenses in secondary aluminum production is at 5%. With the recovery of aluminum products that have completed their useful life, it is possible to reduce global warming and fossil fuel use by around 94% (Çakanyıldırım & Gürü, 2021).
The International Aluminum Institute estimates that about one billion tons of aluminum have been produced worldwide since 1880, and three-quarters of that amount is still used today. Approximately 35% is used in buildings and structures, 30% in electrical cables and equipment, and 30% in transportation (About Aluminium, 2022). 80% of all beverage cans used worldwide are made of aluminum. Beverage boxes are the primary source of secondary aluminum production in the United States (Eroğlu & Şahiner, 2018).
The reasons why aluminum can be used in such a wide sectoral distribution are its lightness, durability (mechanical and corrosion resistance), thermal and electrical conductivity, cheapness, high elasticity, excellent optical properties, easy machinability, spark freeness, aesthetic appearance, easy formability (Eroğlu & Şahiner, 2018).

The aluminum industry is vital in reducing greenhouse gases and air pollutants from transport. It is essential to reduce vehicle weight in reducing the fuel consumption of vehicles. If the lightened cars are moved with electric motors, it is stated that greenhouse gas emissions can be reduced by 94% (Çakanyıldırım & Gürü, 2021). Approximately 25% of the use of aluminum belongs to the production of vehicles. With aluminum-lithium alloys, airplanes can be 15% lighter. Aluminum accounts for 75–80% of modern aircraft (System Aluminium, 2022).
China, the primary aluminum industry leader in recent years, has rapidly increased its production to meet its growing domestic demand since 2000, producing 32 million tons in 2017 and realizing 54% of the world’s total output of 59 million tons. But in China, 93% of aluminum production is powered by coal-fired power plants (Çakanyıldırım & Gürü, 2021).
3% of the world’s greenhouse gases occur in aluminum production (IEA, 2022).
Since aluminum production requires intensive energy use, the effects of production on the environment are directly related to the method of production of the necessary energy. Using alternative sources instead of coal for energy supply in aluminum industry will end many negativities and costs in production, reducing the burden of production on the environment and increasing the possibility of reusing waste.

In aluminum production processes, wastes that pollute the air include particulate matter, fluorite compounds, sulfur dioxide, hydrogen sulfide, and multi-ring aromatics. The particulate matter to which melting plants are exposed consists of dust and smoke produced during melting. Exposures often reach high levels, given the proximity of workers to combustion sources (Çakanyıldırım & Gürü, 2021).
Aluminum, the metal of the 21st century, is essential for a livable world with a Net Zero Goal. Among the five priority sectors in the Carbon Regulation Mechanism at the Border, which will enter into force in Europe in October 2023, the aluminum sector should also turn to cleaner energies in the production process and work towards carbon reduction. China, India, and Australia, the three largest aluminum exporters, will be disadvantaged as they have the highest emission intensity during the energy production phase. On the other hand, Russia and Canada have a competitive advantage because hydroelectric power plants produce aluminum with lower s due to their significant share in electricity production (Climate News, 2021).
Increasing the proportion of aluminum production from low-emission electricity should be a top priority and represent the largest source of potential emissions reductions in the short term. Aluminum producers must continuously improve their production processes to maximize quality while minimizing costs and environmental footprint. The inert anode process is one of the most advanced technologies aluminum manufacturers are working on today. What the inert anode-based reduction process emits into the atmosphere is not carbon dioxide but pure oxygen. An inert anode call states it can produce oxygen for up to 70 hectares of forest (Metal World, 2018). With this work in ongoing industrial trials, aluminum could be a promising way out for the Earth.
References
Çakanyıldırım, Ç., & Gürü, M. (2021). Developments in Aluminum Production Technologies, Environmental Impact, and Application Areas. Journal of Polytechnic, 24(2), 585–592.
Eroğlu, D., & Şahiner, M. (2018). Aluminum in the World and Turkey. General Directorate of Mining Technique and Exploration.
About Aluminum. (2022). https://www.aluminiumleader.com/production/how_aluminium_is_produced/
Climate News, (2021). https://www.iklimhaber.org/tum-ayrintilariyla-sinirda-karbon-duzenleme-mekanizmasi-nedir-ne-degildir-ne-ise-yarar/
IEA. (2022). https://www.iea.org/reports/aluminium
Metal World. (2018). https://metaldunyasi.com.tr/tr/guncel/94/birincil-aluminyum-uretimi-devrimin-arefesinde.html
System Aluminium. (2022). https://www.sistemal.com/aluminyum-ve-havacilik-sektoru/